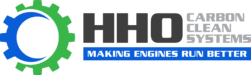
HHO’s Carbon-X is performed using our HHO1500 automated carbon cleaning machine whereby the HHO1500’s output hose is connected to either the air intake system directly or the clean-air-side of the turbo in turbocharged engines.
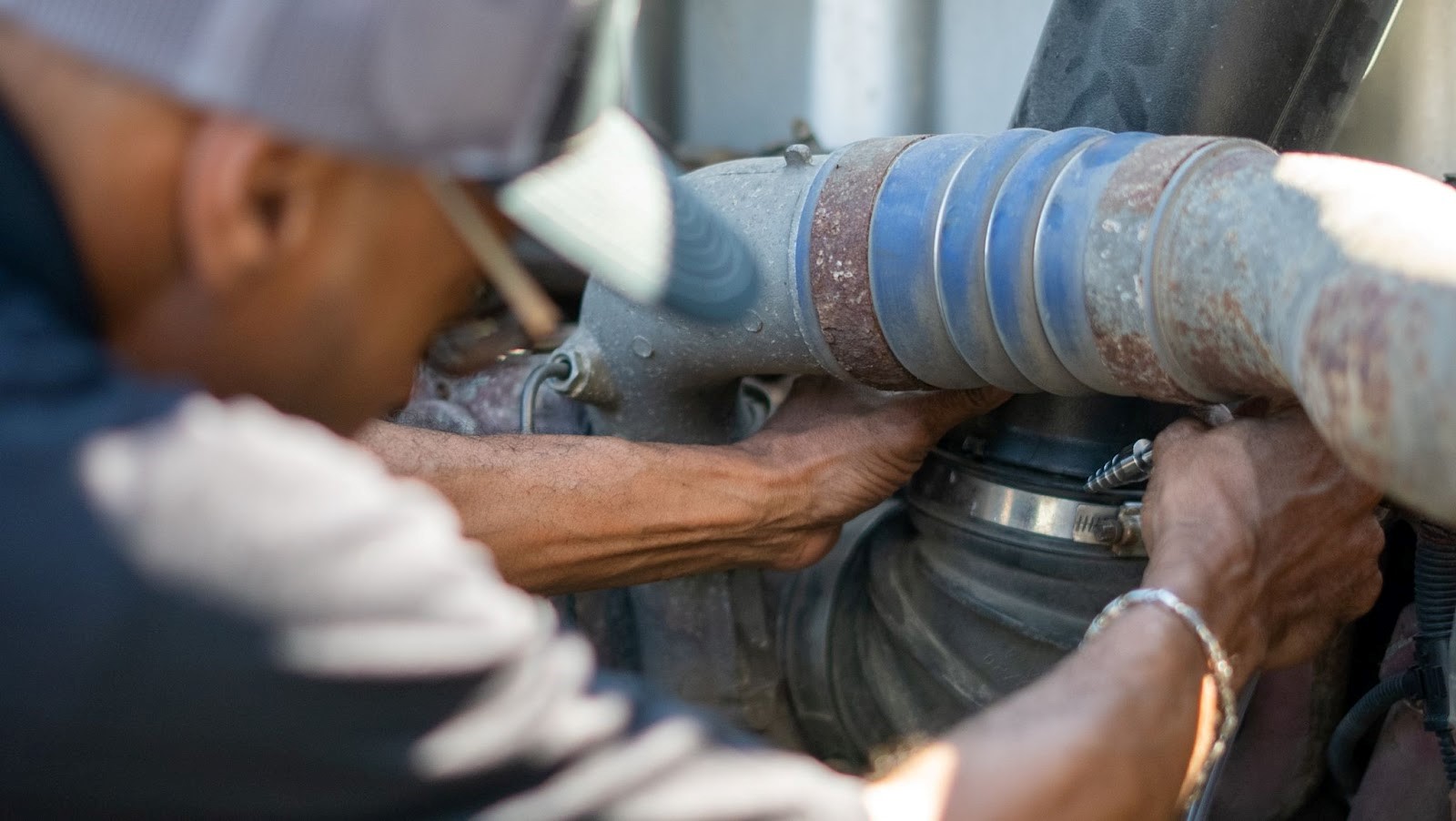
Because many late model vehicles now employ EGR (exhaust gas recirculation) systems, Carbon-X begins removing built-up carbon deposits immediately after entering the intake system, cleaning plenums, throttle body, and intake manifold before reaching the intake valve.
Intake valves sticking, not properly sealing, and/or causing timing and compression issues has become one of the most common maintenance issues pre-combustion-chamber. The implementation of EGR systems has greatly increased these issues along with the move to direct injection in nearly all light-duty vehicles. Previously in gasoline engines, port injection allowed for gasoline’s natural solvent properties to help mitigate and clean carbon deposits from intake valves. Initiating HHO’s Carbon-X in the air intake system provides carbon mitigation and removal at the molecular level, safely carrying carbon through the combustion chamber and exiting the system via exhaust.
Here you can see how excessive carbon deposits have built up on the manifold side of the intake valve. Using HHO’s HydroTorch to simulate the effects of an HHO flame compared with a standard fossil fuel flame, you can see just how effective HHO’s Carbon-X service is at removing caked on carbon deposits.
Moving into the combustion chamber itself, most engines will experience loss of performance and efficiency in a myriad of ways due to excessive carbon buildup. Cylinder walls and piston heads accumulate carbon deposits leading to increased friction and inefficient transfer of energy to the crankshaft. Reducing cylinder wall friction and returning piston head to its designed shape and specification is an efficiency gain that, along with other improvements, combine to deliver improved fuel economy, horsepower, acceleration, and smooth idle.
In gasoline engines, spark plugs can also become inundated with carbon deposits leaving partially or completely nonfunctional. In less severe cases, this can result in rough idle, poor acceleration, and engine fault codes to be displayed on dash readouts. In more severe cases, this will cause timing issues, misfires, and engine knocking.
Along with spark plugs, injector tips also tend to build carbon deposits where they protrude into the combustion chamber. Atomization (turning liquid into a mist or vapor) is key to efficient combustion of fossil fuels, and as carbon builds up near the end of the injector tip, it can cause some atomized fuel to reaccumulate as droplets which are effectively wasted in terms of conversion to usable energy. This can begin a feedback loop where the engine’s ECM realizes that the required power is not being produced and dumps in more fuel to compensate, a portion of which also hits carbon deposits and reaccumulates into droplets where it can’t be burnt properly.
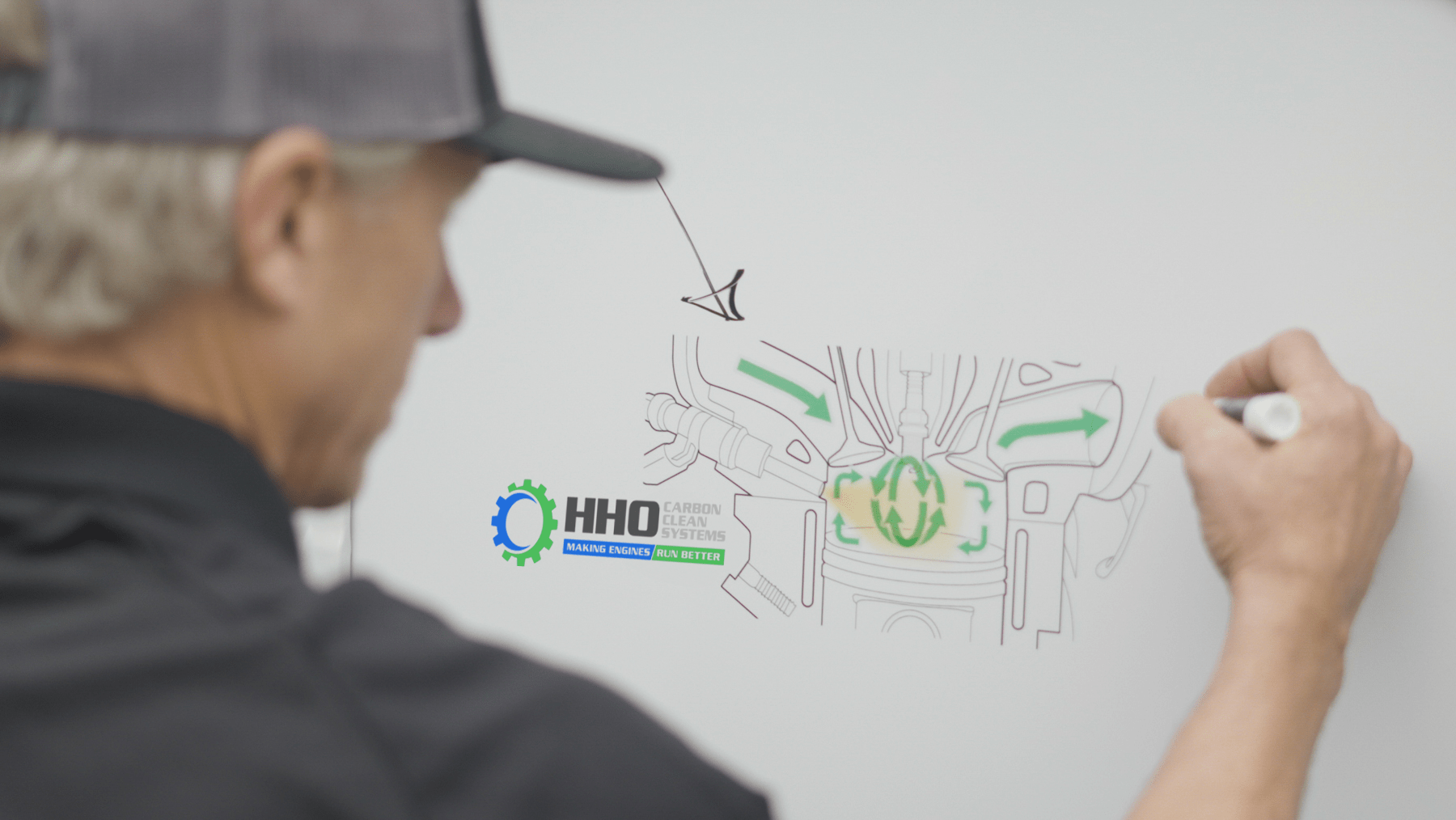
Removing carbon buildup from spark plugs and injector tips solves some of the most frustrating drivability issues that are common as vehicles and engines age. Using HHO’s Carbon-X service as a regular piece of a primary maintenance schedule can not only save on fuel expenses, but provide a much more enjoyable driving experience.
As HHO gas leaves the combustion chamber, delivering to the exhaust-side valves and manifold the same benefits as intake-side components, it will encounter the EGR valve where a portion of exhaust gasses will be recirculated back to the intake manifold. EGRs are relatively low volume systems that remain closed at idle, making it exceptionally difficult to pass enough volume of HHO gas through the system to achieve consistent results. HHO has had success with individual EGR systems and can certainly remove carbon deposits that build up on the exhaust-facing side of the valve, but would hesitate to market our service as an EGR fix due to the inherent design of the systems.
The next component on the exhaust side is the turbocharger. In turbocharged vehicles, whether gasoline or diesel, turbos deliver forced atmospheric air to the engine via a turbine driven by its own exhaust gasses. These turbines are designed with maximum aerodynamic efficiency in mind, and in some cases can spin at 100,000’s of revolutions per minute. Any loss of aerodynamic efficiency within these components can result in drastically decreased power and increased fuel consumption.
Aside from aerodynamic loss, most modern turbochargers employ a variable geometry design (VGT) and rely on tight tolerance actuation to alter the amount of airflow that passes through the exhaust-side turbine, thereby controlling the speed and compression of air forced into each cylinder. Designs vary, but primarily either use veins mounted individually on pivot points or unison ring designs that move veins into and out of position through a fixed ring built into the housing of the turbocharger. In both cases, carbon deposits can build up in the areas meant to move or pivot and prevent actuation. Without the ability to differ the amount of forced air being delivered to the engine, the control module (ECM) again begins to add fuel to each cylinder revolution to make up for the lost efficiency of combustible air.
Removal of these carbon deposits allows proper function and avoids damage that could be caused to electric turbo actuators when electric motors malfunction while trying to actuate turbo components that would otherwise be stuck in position by built-up deposits.
Other than ‘instantaneous fuel usage’ that is sometimes available on late model units, turbo speed and turbo boost pressure are the first consistently measured parameter ID that allows for convenient before-and-after comparison when servicing an engine. HHO’s Carbon-X service regularly improves turbo speed and turbo boost pressure between 20-40% following initial Carbon-X service. Again, these parameter-level, fractional improvements are key in improving overall performance, efficiency, reliability, and longevity for HHO customers.
After flowing through the turbocharger, exhaust gasses continue their journey into exhaust-aftertreatment components. In gasoline engines, this is limited to a catalytic converter. Catalytic converters are designed to reduce pollutants including carbon monoxide and nitrogen oxides, and does so by passing exhaust gasses over rare Earth metals such as platinum and rhodium. This process is reliant on the molecule-to-molecule contact between the exhaust gas and metal ‘monoliths’ or screens. When carbon deposits settle in the catalytic converter and build up on screens and filters, the catalyst is no longer able to come in contact with exhaust gasses and ceases to be effective.
Catalytic converters that accumulate excessive carbon deposits often trigger ‘catalyst deficiency’ codes within the ECM, illuminating dash lights and requiring diagnosis using an automotive scan tool. Assuming that no further mechanical damage has occurred within the catalytic converter, HHO’s Carbon-X service commonly solves catalyst deficiency issues and allows for continued safe operation of the vehicle.
In diesel-engine units a much more complicated system of exhaust aftertreatment has been integrated beginning in approximately 2007. These systems now include three distinct components and are most commonly arranged with the selective reduction catalyst (SCR) coming first and delivering pretreated exhaust into the diesel oxidation catalyst (DOC), which in turn feeds into the diesel particulate filter (DPF). Taken together, these components reduce harmful emissions by mixing diesel exhaust fluid with exhaust gasses to reduce NOx emissions, oxidizing monoxides (CO & NO) into dioxides (CO2 & NO2), and trapping & burning particulate matter to be stored within the DPF as ash.
These components suffer greatly from carbon inundation and are common maintenance or repair items on equipped units. Primary issues in the SCR resemble injector issues within the combustion chamber, as the SCRs primary function is to atomize diesel exhaust fluid (DEF) and pretreat exhaust gasses by chemically removing NOx. If the DEF doser injector tip accumulates carbon buildup, DEF is not properly atomized and mixed, resulting in downstream inefficiencies as exhaust gasses have not been properly pre-treated.
Carbon-X service effectively removes carbon buildup from the SCR and DEF doser nozzle, remedying any downstream effects and ensuring harmful emissions are well controlled within the system.
The diesel oxidation catalyst (DOC) serves much the same function in diesel engines as catalytic converters in gasoline engines, converting monoxides into dioxides via direct contact with screens and filters made of rare Earth metals. These screens, if inundated with carbon deposits, no longer make direct contact with exhaust gasses, leaving harmful monoxides present in tailpipe emissions and likely causing the ECM to trigger fault codes or even derate the engine until issues are solved.
Depending on the particular vehicle’s design, DOC inlet pressure may be used to measure the overall resistance within the DOC and DPF. Taken as a group, inlet pressure, outlet pressure, and differential pressure (pressure difference or resistance) are indicative of the amount of carbon deposits that are built up and causing resistance within these systems. Removing carbon deposits not only allows for proper functioning of the catalytic components, but reduces the resistance and back pressure that accumulates in the system.
Lastly, exhaust gasses reach the diesel particulate filter (DPF), which has become one of the most common headaches for equipment operators and fleet managers over the last fifteen years. DPFs rely on a system of filters, screens, and ports to capture and remove particulate matter from exhaust gasses. Particulate matter is then stored until such time as adequate engine temperatures can be achieved to conduct a passive or forced regeneration, burning of particulates to remove moisture content and pack them in the filter as ash.
There are many opportunities for improper function within this component. If carbon deposits build up on filters, screens, and ports, particulate matter is not properly captured leading to increased sootload and DPF saturation. The ECM would then request a forced regeneration from the operator, potentially resulting in 1-2 hours of downtime as the unit must be parked to complete a forced regeneration. If these requests are delayed and the unit does not reach adequate operating temperatures for a passive regeneration, the problem will persist until eventually the unit is derated or placed in limp mode.
Carbon-X service addresses these core issues before they result in these detrimental effects and can also be paired with HHO’s Enhanced Regeneration service to ensure differential pressure, sootload, DPF saturation, and ash count metrics remain within optimal operating conditions.
Contact Us
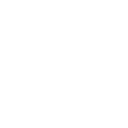
Address
3060 John Puryear Dr
Paducah, KY 42003
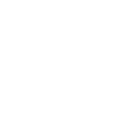